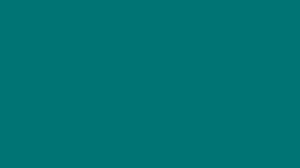
Robotic Automation in the Job Shop
Traditional machine tending requires a lot of manual work. And, frankly, manufacturing businesses can’t afford to move slowly while demand is increasing. Fortunately, the efficiency of machine tending is rapidly increasing, but only with the addition of the right tools and machines.
Thanks to robotic automation, the manufacturing sector can now rely on machines and software to do job shop work in a fraction of the time. And, with advanced Artificial intelligence (AI), these machines can be highly customized to meet the needs of any factory across a wide range of applications, making them a perfect fit for your manufacturing business.
What is Robotic Automation?
If it weren’t for machining technology advancements, there wouldn’t be a manufacturing industry. New technology is constantly changing the production landscape. However, think back to all of the times when your machine operators spent all day using complex machinery only for it to break down or cause injuries.
Now, what if you were to take the human out of the equation?
Automation is taking the manufacturing industry by storm, and now is the time to get ahead of the new industrial revolution. Robotic automation uses robots to perform mechanical tasks seamlessly so your mechanics can focus on more lucrative tasks. Modern robots are equipped with sensors and control systems that allow them to manipulate objects, perform precise movements, and execute complex processes quickly and accurately.
Robotic automation is essential when it comes to streamlining production processes, increasing efficiency, improving product quality, and enhancing workplace safety. To accomplish this, robotic automation assists with many tasks, including:
- Cutting: Automated machinery can handle all kinds of cutting processes, including laser cutting, plasma cutting, and etching.
- Fabrication: Mechanics can turn to robotic automation when constructing components, parts, or structures from raw materials or prefabricated components.
- Assembly: Instead of manually assembling parts, automated machines can assist with the production of complex products that would be difficult or impossible to manufacture as a single piece.
- Welding: Robotic automation can fuse contents together in a safe and controlled environment.
- Packaging: Though essential for the delivery of products, the packaging process is very tedious. Automated packaging means mechanics can focus on maintenance and quality control while the machines address high volumes of packaging.
- Material Handling: Delicate products may be damaged due to human accidents, but robotic automation can ensure that every item is handled appropriately and safely.
By implementing robotic automation, manufacturers can achieve higher productivity, reduce operational costs, and adapt more easily to changing market demands.
Of course, it’s important to be mindful that this technology continues to evolve with advancements in robotics, artificial intelligence, and machine learning, enabling even greater levels of automation and integration within manufacturing environments. That’s where AWR can help.
Benefits of Robotic Automation for the Manufacturing Industry
While everyone needs a little rest, robots don’t! Continuous and precise work brings manufacturers and mechanics a wide range of benefits. And that’s not to say that mechanics aren’t a vital part of the manufacturing process. Robotic automation will still need keen observation before it’s perfected, but these tools can take some of the heavy lifting off employees’ hands.
With that said, let’s take a closer look at some of the benefits robotic automation provides.
Reduced Labor Costs
While the initial investment in robotic automation can be significant, the long-term cost savings are substantial. Robots reduce labor costs by replacing repetitive and labor-intensive tasks with highly efficient and consistent automated processes. Automating tasks such as assembly, welding, and material handling, means manufacturers can reduce their dependency on human labor and lower expenses.
And, job shops that use robotic automation will also notice fewer errors and defects in the manufacturing process. Minimal errors means maximum output. But, just like any worker, machines need a bit of TLC, too. However, the maintenance required for upkeep is minimal and allows for continuous operation without disruption. And, programming doesn’t have to be complicated with the right team who knows the ins and outs of your machinery.
Improved Employee Retention
While the U.S. is among the top manufacturing countries in the world, America fails to lead the pack in manufacturing outputs. The manufacturing industry has a weak link in the States, meaning finding and retaining skilled mechanists is proving to be difficult. So, in order to stay competitive, manufacturing businesses can offset worker deficiencies with robotic automation.
With the addition of robotic automation, employees will have the resources needed to boost their productivity. This increase in production will allow your machinists to improve their efficiency while reducing the feeling of being overworked since the robots are doing most of the heavy lifting (literally).
One misconception when it comes to automation is that these tools can replace current machinists. Instead, they step in to solve efficiency problems and improve the overall quality of work. Plus, a robot isn’t limited to an eight-hour shift. This not only frees up time for employees to do more important work, but it also improves part quality and consistency.
“[Machine tending robots] aren’t taking jobs away from people. What they’re doing is they’re filling spots that we can’t fill with the current workforce that’s out there.”
Kurt Brinson
Director of Manufacturing, B&B Gear and Machine Co.
Increased Profit Margin
Unlike your typical mechanic, robots can work continuously without breaks, fatigue, or the need for rest, leading to higher productivity levels. They can also perform tasks at a consistent speed, reducing cycle times and increasing output, in turn increasing profits.
Plus, robots can operate 24 hours a day, seven days a week, leading to continuous production and shorter lead times. This allows manufacturers to meet tight deadlines and fulfill customer orders more efficiently. And, with continued maintenance and training staff on operations, manufacturers can extend the lifespan of their tools.
Additionally, these machines can be reprogrammed to meet a variety of needs, making them flexible and scalable for all kinds of manufacturing applications. This agility enables manufacturers to quickly respond to market demands, ramp up production during peak periods, and introduce new products with minimal disruption.
Essentially, robotic automation of manufacturing technology makes production easier than ever before, saving teams time and energy throughout the production process. By maximizing operational flexibility, manufacturers can capitalize on market opportunities and optimize resource utilization, ultimately driving higher profit margins.
Enhanced Safety
Robotic automation plays a significant role in enhancing workplace safety within the manufacturing industry thanks to the many tasks that these tools can accomplish. One key aspect is the ability of robots to take on tasks that are inherently hazardous or pose risks to human workers. By delegating these tasks to robots, manufacturers can reduce the exposure of their workforce to dangerous environments, potentially harmful materials, or physically demanding activities.
It’s hard to avoid human error, but perhaps the best way to do so, and to keep workers safe, is to limit the amount of human activity in a job shop. Robotic automation enables manufacturers to implement safety protocols and standards more effectively, thus reducing the likelihood of human errors.
Robots can be programmed to adhere to strict safety guidelines, such as maintaining a safe distance from human workers, operating within specified speed limits, or shutting down automatically in the case of emergencies. These built-in safety features provide an additional layer of protection for workers and help prevent accidents before they occur.
When talking about workplace safety, we often consider incidents that happen on the factory floor. But, long-term and repeated strenuous activity can have health and safety implications as well.
By automating repetitive or monotonous tasks, robotic automation can mitigate the risk of ergonomic injuries and musculoskeletal disorders among workers. These injuries often result from prolonged exposure to physically demanding tasks or awkward postures, both of which are all too common in manufacturing spaces and lead to chronic pain and discomfort. By offloading these tasks to robots, manufacturers can alleviate the strain on their workforce and promote a healthier work environment.
Improved Quality
We’ve mentioned how robots are excellent when it comes to accuracy. Since these machines can be programmed to meet different functions, manufacturers can expect consistent outputs, resulting in higher product quality and fewer defects. They can consistently perform repetitive tasks without variations, ensuring uniformity in the manufacturing process.
Plus, robotic automation enables real-time monitoring and feedback mechanisms that promote proactive quality assurance. Many robotic systems are equipped with sensors and inspection technologies that can detect deviations from expected outcomes and make adjustments on the fly. This capability enables manufacturers to identify and address potential issues before they escalate, thereby preventing defects. A bonus is the increased customer satisfaction when the final product meets a high standard thanks to uniformity in production.
By leveraging the capabilities of robots, manufacturers can increase profits and prioritize safe work environments for their employees, all while improving operational efficiency and productivity.
Overcoming 4 Robotic Automation Challenges
Like any new technology, robotic automation comes with its own challenges. However, before implementing these solutions, it will be beneficial to know what challenges to expect and understand how to tackle them. Afterall, the addition of robotic automation to any job shop is a necessity that introduces a slew of benefits.
System Integration
If you’ve grown used to your current tools, it can be difficult to make a switch to a new system. However, if your current tools are outdated or failing to help you meet your production goals, then it’s likely time for an upgrade.
Fortunately, getting started with new technology often comes with support and training from the manufacturers. For AWR products, your team will be provided with assistance from our experts to make sure you know the ins and outs of your robotic automation system.
System Adoption
We get it, new technology and tools can be intimidating. But, they’re also exciting! The addition of robotic automation opens up any manufacturing business to new production opportunities, but it’s also important to make sure that your team is ready to roll out new technologies.
The latest robotic automation technology is equipped with user-friendly designs, making them easy to learn and operate. With thorough training of each new machine and its features, any mechanic can quickly become an expert in their new tech.
Maintenance
Robotic systems are sophisticated and require regular maintenance to ensure optimal performance and longevity. But, consistent upkeep can bring its own challenges, including the need for specialized knowledge and dedicated time associated with servicing the machines.
However, regular maintenance is necessary when it comes to extending the longevity of the machines in your job shop. That’s why it’s critical to create a maintenance plan that schedules routine upkeep activities during planned downtimes, which should occur during a period of low demand. That way, you can ensure your technology is ready to go ahead of peak seasons.
Additionally, training both mechanics and maintenance personnel in robotic technology is crucial. Continuous education can equip your team with the necessary skills to handle advanced robotic systems efficiently and ensure they continue to function without running into major setbacks.
Machine Safety
All work environments require safety measures in place, and that extends to the tools being used in your manufacturing business. When introducing robotic automation, it’s important to keep in mind that robots can operate with considerable force and speed, which poses risks if there is any interaction with humans. The primary safety concerns include accidental collisions, improper programming, and equipment malfunction.
To mitigate these risks, implementing comprehensive safety protocols is essential. Proper implementation requires regular training and education to ensure all staff members are up to speed and know what actions to take to keep themselves and others safe while working with sophisticated machinery. Additionally, establishing physical barriers, safety zones, and emergency stop mechanisms can further protect workers from potential hazards.
Furthermore, adhering to industry standards and regulations, such as those set by the International Organization for Standardization (ISO) and the Occupational Safety and Health Administration (OSHA), is vital. And, addressing these challenges before they turn into larger problems will help make sure your team is ready to start implementing new robotic automation features and driving productivity.
Applications of Robotic Automation
Robotic automation has revolutionized the manufacturing industry with its diverse applications across various stages of the production process. Whether you’re focusing on precise welds or mass production of a single item, the addition of robotic automation is worthwhile.
Assembly
One of the primary applications is product assembly, where robots excel at precisely fitting components together in a repetitive and error-free manner. Whether assembling intricate electronic devices or automotive components, robots can handle complex assembly tasks quickly and accurately, leading to higher product quality.
Welding
Another critical application of robotic automation is welding, particularly in the automotive, aerospace, and construction industries. Welding robots are equipped with specialized tools and sensors that allow them to perform welds with consistent quality and precision. They can work in challenging environments, such as confined spaces or extreme temperatures while minimizing the risk of defects or inconsistencies in the welds.
Material Handling
Many factories are dealing with delicate products that require a certain level of care. Fortunately, robots are useful for precise and efficient material handling. Whether it's loading and unloading parts on production lines, sorting and palletizing goods in warehouses, or transferring materials between different stages of the manufacturing process, material handling robots streamline logistics operations and improve throughput. By automating these tasks, manufacturers can reduce manual labor, minimize the risk of injuries, and optimize the use of space and resources in their facilities.
Quality Control
Additionally, quality inspection is a critical aspect of manufacturing to ensure that products meet stringent standards and specifications. Fortunately, robotic automation technology that uses advanced sensors, cameras, and imaging systems are an essential addition to a manufacturing team when inspecting products for defects or inconsistencies.
CNC Machining
We can’t discuss robotic automation without also mentioning CNC machining. CNC (Computer Numerical Control) machining uses computer-controlled systems to execute precise machining operations, such as cutting, drilling, milling, and shaping raw materials into finished parts or components. Integrating robotic arms with CNC systems allows these machines to perform complex tasks with greater flexibility and efficiency. Robotic CNC machines can handle various machining operations autonomously, change tools dynamically, and even adapt to changes in production requirements.
These are just a few examples of the myriad applications of robotic automation. From machining and packaging to inspection and quality control, robots continue to play a crucial role in improving efficiency, productivity, and competitiveness across various sectors of manufacturing. As this technology continues to evolve and advance with the growth of machine learning and AI, we can expect to see even more innovative applications that further enhance the capabilities and impact of robotic automation.
Getting Started with Robotic Automation for Machine Tending
The bottom line is that technology is improving efficiency across every aspect of businesses, and this continues to be true in the manufacturing space. And, thanks to robotic automation, manufacturing businesses can not only boost productivity but prioritize the health and safety of their mechanics while boosting ROI.
If you’re ready to grow your manufacturing business by dipping your toe in the automation pool, Automation Within Reach is your solution. Our user-friendly interface takes the complexity out of automated machine tending and allows you to handle a variety of parts on a single machine. With this technology in your lineup, you can reduce your mechanists’ workload by letting the AWR machine tackle repetitive tasks without the errors caused by manually loading.
AWR will help you to reduce labor costs and increase profit margins in your job shop. If you’re interested to see if one of our machine-tending solutions can benefit you, contact us, and we'll let you know which one will be the best fit.