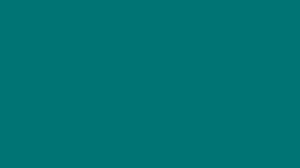
FAQs
FREQUENTLY ASKED QUESTIONS
The robot batteries ("C") have died, and need replaced. Locate and follow "Remaster from a battery loss" manual found on the AWR distributor portal
The robot batteries ("C") are low, and need replaced. Locate document on "How to Change Robot Batteries" at link below.
Locate the HMI screen power switch located on the back side of the unit. Press and hold button for 15 seconds, then release. Then press button again to start the reboot cycle.
Locate the HMI screen power switch located on the back side of the unit. Press and hold button for 15 seconds, then release. Then press button again to start the reboot cycle. If this does not fix the problem contact customer service to setup getting a replacement unit shipped out.
This usually means that there are two instances of the HMI application opened at the same time. Close the application and then reopen.
If a fault will not clear on the computer screen then go to the robot teach pendant screen for more detail on what is preventing fault from clearing. Contact customer support for further assistance.
Confirm the pushbutton next to L&G Computer screen is released by being pulled outward.
If E-Stop button is released, confirm teach pendant cable is not damaged. Replace Teach pendant cable if Alarm will not clear, and no other Alarms are present. If other Alarms exist, check all fuses in robot cabinet on E-stop board. Call Support for further troubleshooting of other system alarms.
The Drawer is unlocked.
A vise sensor for the specified vise is not reading correctly. Either there's a misload, the vise sensor needs adjust, or the sensor needs replaced. See Installation manual for how to install, and adjust vise sensors.
It the robot attempts to place a part in the regrip area with a empty gripper, that's saying a gripper sensor has failed or the sensor trigger has moved from set position.
Mist is the #1 cause of false scanner faults. Other than mist you can clean the scanner lens with a damp cloth, or a lens cleaning towel, and confirm area is clear of obstructions.
An object is now setting closer to the area scanner zones causing unexpected interruptions.
The robot power is turned off. Confirm both Main, and robot controller disconnects are turned on.
Close all drawers. Confirm HMI settings are set correctly. Ready and open a new drawer and continue.
The part unloaded from the machine was not loaded by the robot. Send Robot to Home, and the part will be removed from the gripper.
The gripper pins are not set correctly, and the overtravel switch is being detected.
The RC and DC both have area scanners that correlate to the robot speed, they will run slow if something is in the slow zone which is another zone set just outside of the stop zone. Each product has there own unique spot to change the speed. The DC has one overall speed setting located to the left of the recovery button on the right hand side of the screen. The RC speed setting is located on the screen you'd recover the robot on the bottom of the circle. It has two speed settings; one of load/unload and robot cell speed. You can toggle between the speed sets but tapping on the running man logo, the max cell speed is 100% and the max load/unload speed is 150%.
There are two instances of the application open on the HMI. Close out the application, and reopen.
The application has crashed and stopped communicating with the robot. Close the application and reopen.
The gripper pins are set incorrectly.
Verify all mechanical components attached to the robot are secured properly.
The centerline position needs adjusted.
Something mechanical has came loose. Check the grippers, gripper fingers, and gripper pins for any loose hardware.
If the light on the area scanner is yellow, then the robot will run at a reduced speed. Locate and remove the object is in the slow down zone to continue at normal speed.
When the alarm information is not displayed, you must review Robot teach pendant screen for more information on the fault.
A Dirty scanner lens is likely the cause. Sick scanners have a yellow dirty lens indicator. If this is blinking wipe down lens with a damp cloth using water, or a lens cleaner.
Confirm - Machine is in Auto, Has No faults, Is At Home position, Has a program end signal active, and Door is in correct location.